After years of hard study, following an intense internship in the pharmaceutical industry, submitting your carefully prepared dossier to the Federal Agency for Medicines and Health Products, you do make a small dance of joy when you receive your mail approving your application to become a Qualified Person. You will also receive a unique tracking number published in the Belgian Official Journal. In short, a milestone in your career and one you can be proud of.
Not everyone starts to work as a QP for a pharmaceutical company at the beginning of his/her career, but I have had this opportunity. There is a lot of responsibility involved, but unfortunately that is not always recognized by everyone. Almost every QP has probably heard: ‘Being a QP is like being a bird in a golden cage’. Or what about this one: ‘Actually you don’t have to do much anyway, it is just about putting your signature’. The first time I received a similar comment, I cringed for a moment. After multiple hours of reviewing batch records, deviations, change controls, QC results, and filling out checklists, I was hit hard with the fact that there is a perception that I am ‘just’ putting my signature. Not to mention the time pressure that is often involved. There is no room for uncertainties or questions.
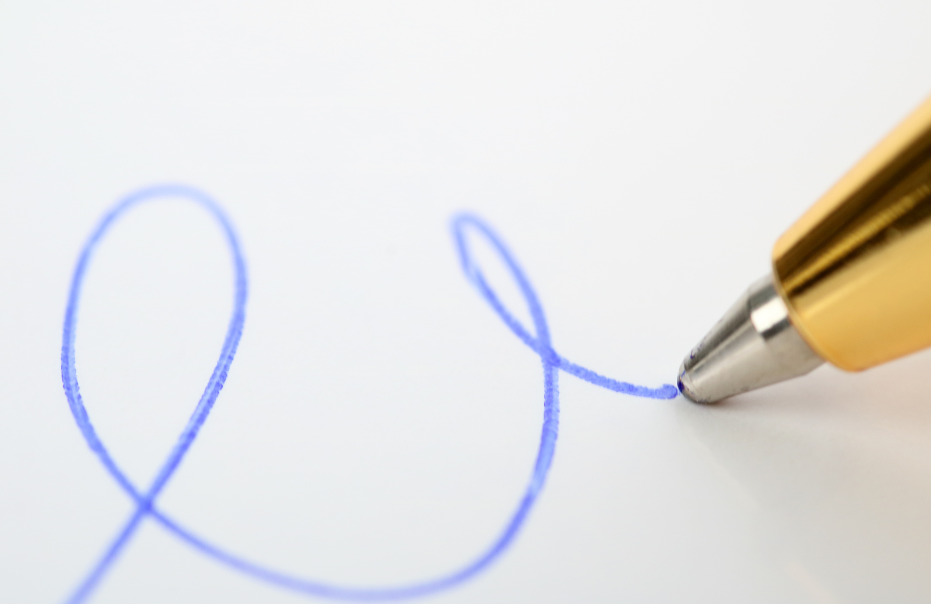
With this blog, I would like to thank all QPs, as well as all other QA people who do their part in the release and certification of clinical and commercial batches.
With that so-called signature, you ensure the quality of the pharmaceutical product produced and thus the patient’s safety, regardless of whether it is a human or an animal. A responsibility that should not be minimized. In order to be able to give such a signature with confidence, it is important that you create an overview of the building blocks of your product and what unexpected problems these building blocks have encountered during the production process and may have affected the quality of the product. To ensure the quality of your product, it is obvious that you should check some clear criteria, such as the sterility of an injection liquid. In addition, there are also less obvious criteria that can affect product quality such as personnel training, supplier qualification, … Obviously, you cannot go checking every link that contributed to the quality of your product on your own as a QP or as a QA release team. Quality must be built in through well-functioning processes, validated standards, … that extend beyond just the QA department and the QP. A lot of issues are prevented or already identified and evaluated before the product batch reaches the QA release team or the QP. But as long as there are people involved in the production process, there will also be human errors. Hence, each review step guarantees production quality a little more each time, regardless of which department performed this review. Release and certification of a product batch may be regarded as that very last round of review before the product actually reaches the patient. And although it is the last, it is no less important for that.
In summary, every link and every person who does their part to ensure good quality and thus puts the patient’s well-being and safety first, may be seen, recognized and thanked. From operators, QC lab technicians, maintenance personnel, to quality personnel, you are more than that number in your personnel file. And for all QPs, you are more than that number in the Belgian Official Journal!