Since the implementation of the Medical Device Regulation (MDR) in Europe, companies have had to maintain and execute a post-marketing surveillance (PMS) procedure. This systematic process involves collecting and analysing data on the performance and safety of medical devices after they have been released to the market. The primary goal is to help manufacturers identify and address potential issues that may arise during actual use, monitor the market for known risks, and identify new risks.
To achieve this, the PMS process interacts heavily with other processes, both in terms of data collection (input) and actions taken (output).
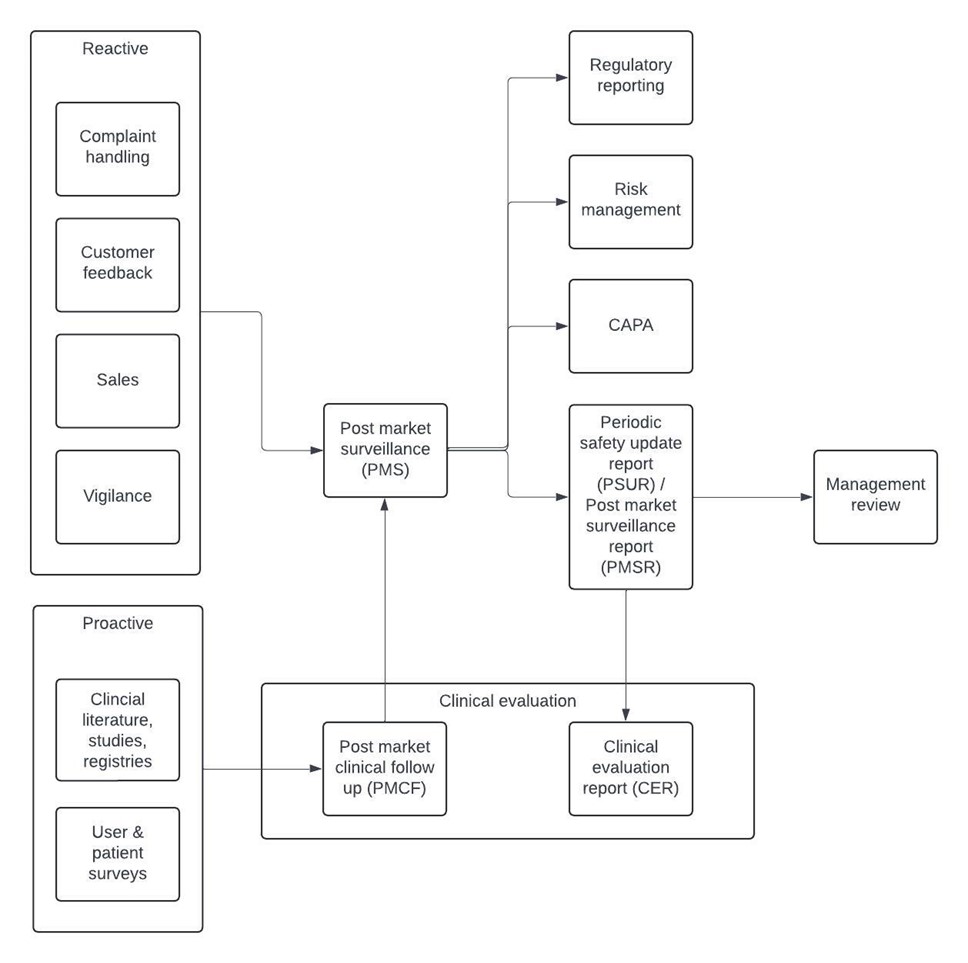
Figure 1: visualisation of the information flow centered around the Post-Market Surveillance process.
The Need for a Common Language
Given the interdependence on a wide range of processes, a common language between these processes is essential. The easiest way to achieve this is by adopting the IMDRF-coding throughout all relevant processes in the company.
IMDRF-coding (of which a partial example can be viewed in table 1 below), developed by The International Medical Device Regulators Forum (IMDRF), is a coding system designed to streamline the reporting and analysis of medical device incidents. It enhances the effectiveness and efficiency of medical device performance and safety. This standardization:
- Ensures that all stakeholders, including manufacturers, regulators, and healthcare providers, use consistent terminology, reducing misunderstandings and discrepancies in data interpretation.
- Minimizes the risk of errors and omissions in incident reports, leading to more precise and comprehensive data collection.
- Aligns with international regulatory requirements, helping manufacturers meet stringent post-market surveillance obligations under the MDR and other global regulations.
- Enables manufacturers to categorize and analyse incident data, identifying patterns and emerging issues faster and more efficiently.
- Improves the clarity and effectiveness of communications between manufacturers, regulators, and healthcare providers.
- Ensures manufacturer PMS processes are aligned with global best practices.
Tabel 1: Partial example of IMDRF Annex A. (source: Terminologies for Categorized Adverse Event Reporting (AER): terms, terminology and codes | International Medical Device Regulators Forum)
Level 1 Term | Level 2 Term | Level 3 Term | Code | Definition |
Manufacturing, Packaging or Shipping Problem | A02 | Problem associated with any deviations from the documented specifications of the device that relate to nonconformity during manufacture to the design of an item or to specified manufacturing, packaging or shipping processes (out of box problem). | ||
Product Quality Problem | A0201 | Problem associated with an inherent device characteristic that is not satisfactory as specified or delivered. | ||
Dull, Blunt | A020101 | Problem associated with a device not being as sharp as intended or expected. | ||
Nonstandard Device | A020102 | Problem associated with the device that does not meet the specifications or requirements for which it was manufactured (e.g. materials, parts, manufacturing process). | ||
Defective Component | A0202 | Problem associated with a device component having flaws of dimensional deviations greater than acceptable for the intended use. | ||
Defective Device | A0203 | Problem associated with having flaws or dimensional deviations greater than acceptable for the intended use of the device. | ||
Device Damaged Prior to Use | A0204 | Problem associated with packaging or shipping damage prior to the use of the device. |
Extending IMDRF Coding Throughout the Company
Instead of using this coding solely for communication with external stakeholders, a much smoother process can be achieved by extending this “language” throughout the company. This would include:
- Logging complaints and feedback in categories aligned with IMDRF.
- Using the IMDRF coding as a foundation for building your risk management processes.
- Reporting using the IMDRF coding in all subsequent processes (PSUR, Management review, CER).
Adopting a common language across the company would save time and improve clarity, ensuring that everyone is on the same page and working towards the same goals.
To ensure implementation simply writing the necessity into SOP’s is, ofcourse, not enough. To implement such a change, we must be aware of the training of employees which will be working with this IMDRF coding, and the integration into the existing data management systems. A common challenge is the resistance of employees which are used to working with the old system and don’t recognize the benefits the new system offers. The best way to get these employees on board would be to include them, from the start, into the implementation process. Gather their feedback and provide continuous support to deliver a smooth transition.
Future trends
Full IMDRF implementation not only delivers immediate efficiency gains but also prepares a PMS system for a future where data gathering will be more AI based. A common coding system throughout the various processes of the company would allow for a smoother transition to a more automated way of working.